Some time ago I came into possession of a well-made bagpipe of undetermined origin that did not behave properly. The tenor drones wanted to tune very low on the pin and any attempts to get them to tune higher resulted in a very rough, coarse sound. I tried just about everything I could think of and finally isolated the problem. The tuning chambers were huge. I slide a brass sleeve into place and the drone immediately and dramatically improved its sound and behavior. It tuned at the hemp line and the coarseness disappeared. I have also sleeved the bottom section of bass drones to improve performance.
My only advice in these matters is if you can’t afford to throw it away and have a replacement part built, don’t mess with it.
I do not recommend radical experimentation unless you are highly skilled, both as a piper and in machining. In my experience, there are no guaranteed results. If you have a drone that is rough sounding, or has excessive "growl" I would first experiment with various reeds to minimize or eliminate the problem. If the problem cannot be corrected within your own abilities or reach thereof, I would be inclined to abandon the drones in favor of a better performing set.
There are many tales of drone designs or flaws having an impact on drone performance. One of the silliest is that manufacturers strive for a rifling effect, to twist the air as it ascends the drone. Rubbish! (Scottish termonology for "bull") Any such marking on a drone is accidental scoring due to faulty tooling or workmanship. The inside bore should be smooth, without checks, burrs, chips, chatters, or uneven walls. This last flaw is caused by inferior boring tools or methods. I have witnessed many drones that had a "bubble" half way down the bore. This may not have an overwhelming negative effect, provided the bore is smooth. If the bubble is rough and uneven, then sound problems will be apparent.
Modest roughness in the inside bore may or may not present a problem. If one is so inclined the bore can be polished smooth. I should warn that any attempts to alter the inside of the drone can severely damage the drone, requiring costly repair or replacement. I am aware of one individual that split his Henderson drone in such an attempt.
I like to give the bores a healthy dose of bore oil in advance of any polishing. This restores some of the flexibility within the wood. I rig a wire probe with "000" grade steel wool wrapped around the probe end and doused in bore oil. I insert the other end of the probe in a hand held power drill and gently, slowly, ease the probe through the entire length of the section in hand. You can best judge your progress by how much resistance the probe is experiencing. If the resistance is too great, you can damage the bore or split the drone. It's better to start with a small amount of steel wool and increase a few strands at a time until the desired tension is felt and enough pressure is created to burnish the oil into the Blackwood. Cautiously following this method, you can polish most bores to a shiny, smooth finish.
Sometimes, tuning chambers will wear unevenly or they have been bored incorrectly by the maker. You will notice that the hemped tenor does not move smoothly and evenly through the tuning chamber. It is inclined to be tight in one spot and loose in another. If this becomes a problem, they should be entrusted to a professional bagpipe maker for re-boring. This is not a job for an amateur or for amateur tools.
In order for drones to perform at their peak, the top section of bass and tenor drones should be fully extended to the bottom of the hemp line on the tuning pin. This allows for the greatest use of the tuning chamber, producing full resonance. Quite noticeably, the same drone, differently addressed to tune low on the tuning pin, will sound dull and lifeless. There are no sound issues involving where the mid-section tunes on the bass bottom section. It's fine for the mid-section to tune low on the pin provided no other issues exist.
A number of items contribute to the drone tuning in the proper position. First of all is the selection of reeds. The synthetic reeds come in a variety of shapes, sizes and materials. Some are better suited for a particular make of bagpipe than another. All of these reeds come with the manufacture’s instructions for adjustment.
If you play cane reeds, the narrower reeds are generally sharper in pitch than fatter reeds. Reeds with shorter tongues are sharper than reeds with longer tongues. Reeds seated deeper into the reed seat will incline the drone to tune further rather than nearer to the base of the tuning pin. We will discuss working with reeds later.
Some drones tune in the minimum performance area as a result of design. Let’s take the tenor drone. Performance starts somewhere in the stock. Then we have the reed seat, the bottom section length and bore, the width and depth of the top section tuning chamber, the small bore within the top section, the bell, and finally the bush exit bore. All of these, along with other characteristics of the particular reed, work in concert to determine drone sound and performance.
To correct or improve the sound and performance of a drone, beyond reed selection or manipulation, is sometimes art and sometimes science. All the internal and external dimensions are working in concert with one another and to adjust one such dimension may have a positive or negative effect on sound and performance.
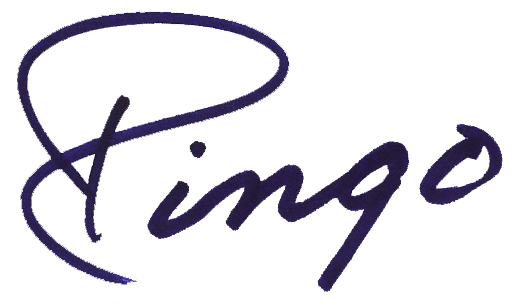
Tips on Drones