Is a drone just a drone? Are all drones created equally? Henderson, Lawrie, Glen, Robertson, Thow, Gillander, MacLeod, Hector Russell, Starck, Kintail, Sinclair, Hardie, McDougall, McCrae, and the list goes on and on and on.
One of the more frustrating experiences of a novice piper, or their parents, is to make their first bagpipe purchase. Much of the information passed from piper to piper regarding bagpipes is based on the personal preferences or prejudices of these individuals, many of whom regale in making general, broad, and largely unsubstantiated, statements on these matters. Of course, they are perfectly entitled to do so, however herein we will tread more softly.
How is one set of drones considered superior to another? Did some manufacturers make both good and not so good drones? Is the wood today as good as the wood used in the old days? What role does craftsmanship play? What about copper sleeves? What about plastic? Why doesn't everybody just copy the best drone and be done with it? These questions exist to keep pipers engaged in lengthy debate and exchange of fact, fiction, lore, and supposition.
Discounting the other factors at play in producing "tone," there are many physical aspects of the drone that will affect the sound produced. There are four different bores in a tenor drone, plus a ring cap at the top of the drone with a particular bore. Even the slightest change in one of these bores will impact the production of sound and the performance of the drone. In the bass drone, there are two additional bores in the "mid-joint". Consider these additional factors:
1. The overall length of each section
2. The depth of the reed seat
3. The various thicknesses along the walls of each section
4. The length of each tuning chamber
5. The type of wood or alternative product used
Although not directly a component of the drone, the care and skill in applying hemp to the various sections can be a major factor in the sound and performance of your drones. As silly as it seems, I have seen pipes that were poorly hemped and loosely joined that were reluctant to perform as they should. Applying the hemp properly made a world of difference.
I have also witnessed foreign objects present in the drone, obstructing both sight and sound. I inspected one fellow's poorly performing bagpipe to find a spider's nest in the top section of his bass drone. I don't know who was more surprised, the piper, the spider, or me. Regular inspection of your drones is necessary to ensure maximum performance. A tip on applying hemp; always rosin the first twelve inches or so of length of hemp that will be against the wood. The rosined hemp sticks to the wood and will prevent the hemp from turning independently. If you do have a problem with hemp turning on the pin, remove it immediately and re-hemp. Be extremely careful if the sections resist separation. Many a good bagpipe has been damaged and broken during such an ordeal. Dry the sections completely using a hair dryer set at "low" temperature. When the hemp is completely dry, the sections should separate easily.
The Great Highland Bagpipe has two tenor drones and one bass drone. The purpose of the drones is to supply a background harmony to accompany the melody being played on the chanter. Drones are tuned to the chanter by adjusting the overall length of each drone. The pitch of the drone is sharpened by shortening the overall drone length, and flattened by increasing the overall drone length. The length is adjusted by moving the various sections across mated pieces.
The tenor drone is comprised of a lower section and upper section. The lower section delivers air directly from the reed, through a straight bore, into the upper section. The upper section has a wide bore or tuning chamber. At the top of the tuning chamber is a narrower section. This delivers air to the top of the drone, called the bell. The bell is covered by a ring and ring cap which has a sound hole. This sound hole is the same diameter as the narrower tuning chamber of the top drone section.
The bass drone has an additional component called the "mid joint". This section has both a tuning chamber and a smaller straight bore, which delivers the sound into the top section of the bass drone. The various components of both the tenor and bass drones are followed by all manufacturers, however the specification of lengths, diameters, wall thickness, etc, varies greatly from maker to maker. It even varies greatly from bagpipe-to-bagpipe of the same maker! And no small wonder. Although some changes were no doubt initiated deliberately by a maker, other changes crept into the manufacturing process unbeknownst and perhaps undetected. The woods used in the manufacture of bagpipes are generally the hardest woods on the planet. These woods took a terrific toll on machining tools. Every time a tool was sharpened, a small change occurred in the finished product. Every time a maker retooled, there was the risk of small variances.
We can also examine both old and new pipes and see the effects of crude tooling. They have left their signatures by way of ridges, chatter-marks, uneven bores, burrs, torn combing, and scoring. It is best to shy away from bagpipes that bear these signatures. Although they may not necessarily affect the tone of the bagpipe, they will undoubtedly affect the resale value of your bagpipe.
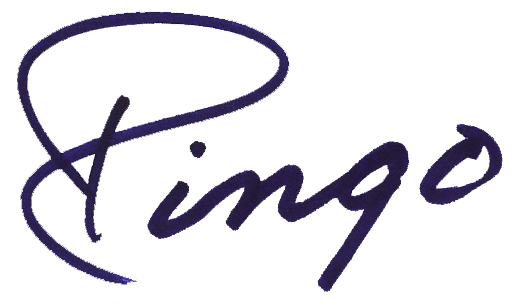